By Bill DeVries
The Biden administration recently announced that Intel will receive $8.5 billion in funding to ramp up U.S. manufacturing of semiconductors.
These investments will help rebuild a previously declining industry that's critical not just to the American economy, but also to our national security. But money alone won't reverse the decades-long slide. American companies and policymakers must account for, and adapt to, the unique challenges facing U.S. chipmakers.
For decades, American policymakers watched idly as the U.S. semiconductor industry collapsed in slow motion. Over the past 30 years, East Asian countries -- namely China, Taiwan, and South Korea -- captured the majority of global semiconductor production, in large part because they heavily incentivized and subsidized their chip industries.
The United States once manufactured 37% of the world's semiconductors, but in the past three decades, the figure has fallen to 12%. American companies lost much of the human capital that's essential for manufacturing advanced chips at scale. Skilled workers retired, or shifted to other industries. Nobody replaced them as factories moved abroad.
Congress took action by passing the CHIPS Act in 2022, allocating $53 billion for domestic semiconductor manufacturing, R&D, and workforce development, as well as $24 billion in tax credits for manufacturers through the end of 2026.
Companies like Intel and Samsung are stepping up and constructing new manufacturing plants in Ohio and Texas. But chipmakers are struggling to find workers with the necessary skill sets to build and operate these factories.
Fixing that skills-gap challenge will require partnerships between industry, academia, and government.
Last spring Micron announced the Northeast University Semiconductor Network, a partnership of over 20 colleges and universities committed to getting students ready for jobs in the domestic industry. In 2022, Purdue University launched a first-in-class Semiconductor Degrees Program and partnered with companies like Lam Research and my own, Dassault Systèmes, to ensure graduates have the training needed to succeed.
Reskilling the workforce -- through on-the-job training, professional development courses, and other hands-on training programs -- can help people pivot within companies or into the semiconductor industry with new skills in tow.
Incentive packages could help move talent from areas rife with semiconductor expertise -- think Silicon Valley in California -- to seed workforces in up-and-coming regions.
We can also get more out of our workforce with more efficient systems. Take "virtual twinning," a process already being used in medicine, construction, and municipal planning. This technology creates a digital replica of real-world processes and physical objects. The digital twin can run simulations testing ways to increase efficiency without the need for physical prototyping and testing.
These digital replicas can simulate an entire manufacturing plant and all the actions taken throughout production, so planners can answer any "what if" scenarios before implementing real-world changes. A manufacturing facility could workshop new production lines, logistics, shipping, and more, all without disrupting day-to-day operations and while enhancing safety, productivity, and quality of life for workers.
With virtual twinning, itself a semiconductor technology, we can prototype new microprocessors, chips, and other semiconductor electronics that are faster, more durable, and more efficient.
Machine learning and artificial intelligence tools offer similar promise for companies to learn lessons in the virtual world that are immediately applicable to real-world manufacturing.
With new incentives to support domestic manufacturing and promising emerging technology, U.S. companies could chip away at China, Taiwan, and Korea's edge in semiconductors.
Bill DeVries is the vice president of North America customer solution experiences at Dassault Systèmes. This piece originally ran in The Dallas Morning News.
Manufacturing chips in the U.S. needs a particular set of skills
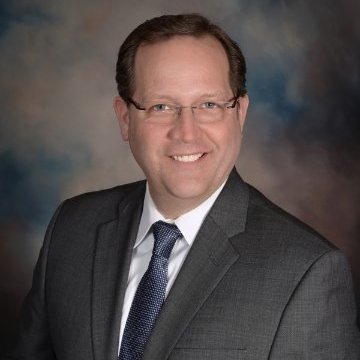
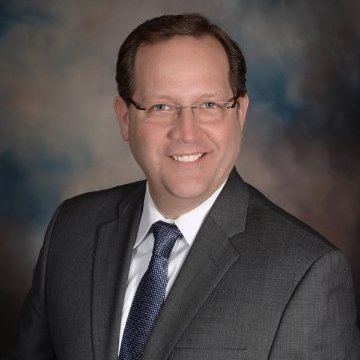